3D Printing: Manufacturing Revolution Through Revolutionary Manufacturing
3D printing has taken the world by storm. From small trinkets, to gargantuan aviation equipment, to biological material including human skin and tissue; 3D printing’s near boundless realm of applications makes it an ideal solution for virtually any unique manufacturing endeavor. A process nearly 40 years in the making, 3D printing, and additive manufacturing in general, has come a long way from its beginnings as simply a prototyping technique. We now have the ability to 3D print anything from baubles to buildings and beyond and this burgeoning industry’s potential is only increasing.
Uniquely Versatile Manufacturing Potential
A prime example of the manufacturing scope of 3D printing is the work being done by scientists at the Department of Energy’s Oak Ridge National Laboratory. Oak Ridge has consistently been at the forefront of 3D printing possibilities, using the technology to create a Shelby Cobra sports car, a fully functional excavator, a house/car energy system, and an Army Jeep.
More recently however, they created the world’s largest 3D printed object when they produced a 3D printed version of a “trim-and-drill” tool used by Boeing to build the wings on its passenger aircraft. After 30 hours of printing, the behemoth tool was about the size of an SUV weighing in at 1,650 lbs and measuring 17.5 feet long, 5.5 feet wide, and 1.5 feet tall. As impressive as Oak Ridge Labs' accomplishments are, the potential of 3D printing extends much further into a wide array of industries.
Medical
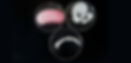
3D x Bioprinting: Regenerative medicine scientists at Wake Forest Institute for Regenerative Medicine created a 3D bioprinter (Integrated Tissue and Organ Printing System), that can produce replacement tissues strong enough to endure transplantation. They were able to print ear, bone, and muscle structures that, when implanted into animals, matured into functional tissue and developed a system of blood vessels. Madrid’s Universidad Carlos III has even created a prototype for a 3D bioprinter that can print totally functional human skin for applications in trauma and burn treatment, cosmetic treatments, and research. As amazing as some of these applications are, the possibilities are really only just beginning; in the coming years, some medical professionals are eyeing the potential to be able to 3D print fully functional organs.
3D x Human Heart: In pursuit of that goal, Nicholas Cohrs, a graduate student at ETH Zurich, successfully created a soft artificial heart crafted entirely from silicone, scaled to the proportions of the human heart. This creation fundamentally works and pumps blood in the way that a natural heart does but has one critical drawback: it can only sustain its function for approximately 3,000 beats which would equate to about 30-45 minutes of lifetime. After that, the material can no longer withstand the strain and disintegrates. This outcome, however, was expected at the outset of the experiment. Cohrs explains: “This was simply a feasibility test. Our goal was not to present a heart ready for implantation, but to think about a new direction for the development of artificial hearts.” While the technology has yet to progress to the point that we could expect an actual transplantation to be successful over time, this work is nonetheless an exciting stepping stone towards that end.
3D x Prosthetics: With 3D printing, prostheses that once cost upwards of $100,000 using traditional methods can be available for as little as $1000 and under. Companies like the Openhandproject and e-Nable are even able to offer free prosthetics to those in need through donations and the savings that 3D printing technology affords them. Those savings don't imply an inferior product; due to the precision of 3D printing, doctors and helthcare professionals are able to generate prostheses that fit the exact dimensions of their patients to ensure maximum effectiveness.
3D x Implants: When it comes to designing implants to replace a functional part of the body, there are two primary considerations: 1) The implant must be accepted by the body and 2) it must reproduce the function of the original part. 3D printing helps achieve both goals by allowing doctors and scientists to precisely craft an implant to fit the constraints in the given subject’s body while also controlling the substance to make sure it is strong enough and capable of sustaining the function of the body part that it is replacing. CSIRO’s Lab 22 created the first 3D printed sternum and ribs to save a patient that had to have his sternum and part of his ribcage removed as a part of cancer treatment. Due to the unique needs and constraints of the situation, 3D printing provided an ideal solution.
3D x Dental: With 3D printing, there is no longer any need for dentists to keep and archive physical molds of his patients’ teeth or for patients to have to endure the uncomfortable process of having a mold made. With a 3D scan, records can be preserved digitally and the molding process becomes much less invasive for the patients. This allows dentists to create 3D print plaster models, orthodontic appliances, positioning trays, clear aligners, and retainers easily as needed to treat their patients.
3D x Pharmaceuticals: Pharmacies may soon be a thing of the past; within a few years, it may be possible to 3D print your own specialized pharmaceuticals from the comfort of your own home. The theory is that at-home users could buy the 3D printer hardware complete with a set of water bottle-sized reactors and purchase specialized chemical compound "ink" packs depending on the requirements of the print. The technology has already been demonstrated as viable; in August of 2015, Pennsylvania-based Aprecia Pharmaceuticals received FDA approval on their 3D printed drug “Spritam” (levetiracetam) used to treat epilepsy. The printed drug is not only approved for use in the same way as conventionally manufactured drugs but, due to the 3D printing process, is also able to dissolve much faster (as shown below).
Veterinary
3D printing’s medicinal value isn’t limited to humans though; it also has a wide range of applications in veterinary medicine. It has generated legs for dogs, feet for ducks, jaws for turtles, “horse-thotic” shoes for horses, and beaks for birds like toucans and even a bald eagle named Beauty.
In a particularly touching story, Beauty the bald eagle was severely injured after being shot in the face by a poacher at the age of six. The top half of her beak was destroyed and as a result, she was not able to feed or bathe herself. When found, Beauty was emaciated and would likely have died had it not been for the efforts of animal rescue workers that found her and
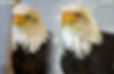
nursed her back to health. As a part of an initiative at the Birds of Prey Northwest ranch in Idaho, raptor specialist Jane Fink Cantwell and mechanical engineer Nate Calvin worked with a team of scientists, engineers, and even a dentist to design a nylon polymer beak that could be affixed to Beauty’s face. Using 3D printing technology, the team was able to print the beak design and affix it to Beauty, allowing her to feed and bathe herself and enjoy a life much more similar to the one she enjoyed before she encountered the poacher.
Architecture
Using 3D printing, architects and engineers are able to quickly and cost-effectively create scale models of complex designs, providing a basis for discussion among peers and a tangible demonstrative device for use in proposals. Before 3D technology was widely available, creating scaled architectural models was a tedious and time consuming process that required a lot of math, a variety of materials, and precise hand-measurement
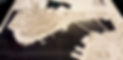
and construction that ultimately yielded a limited and fragile product. With 3D printing, all the architect must do is take the CAD file that they’re already using to create designs, apply it to the 3D printer, and wait for the print. Ultimately, they're left with a precisely scaled model of the given project in a fraction of the time it would have taken to build by hand.
Construction
There have already been multiple buildings created around the world entirely through 3D printing and that trend is showing no signs of slowing down. The technology has truly enamored some; Sheikh Mohammed bin Rashid Al Maktoum, Vice President and Prime Minister of UAE and Ruler of Dubai has stated that Dubai aims to have 25 percent of all its buildings based on 3D printing technology by 2030. The benefits that 3D printing provides to the construction industry are staggering; 3D printing is estimated to cut construction costs by 50-60 percent, labor costs by 50-80 percent, building time by 50-70 percent and will reduce waste produced during construction operations by 60 percent.
Culinary
As strange as it may seem, 3D printing has even been applied to the culinary industry. One restaurant, London-based “Food Ink,” offers an entirely 3D printed experience. From the furniture to the menus, cutlery, and even the food, every aspect of their dining experience is created using 3D printing. Other restaurants have also adopted 3D printing as a compliment to their otherwise traditionally prepared dishes. Melisse, a Santa Monica-based two-Michelin-star restaurant, uses 3D printing to craft croutons in various designs for their French onion soup and to add a new-age flair to other classic dishes. At Barcelona-based “La Enoteca,” Chef Paco Perez creates his dish “Sea Coral” using 3D printing to craft an intricate sea coral design from a seafood puree to which he adds caviar, sea-urchins, hollandaise sauce, egg, and foam of carrot to complete the dish.
3D printing’s culinary potential isn’t limited to the aesthetic; it also has a myriad of nutritional benefits. For instance, some senior living facilities in Germany have begun using 3D printing to create what they call Smoothfood, a type of food that is made using pureed fresh ingredients – including asparagus, meat, and potatoes – and then printed into solid, yet easily dissolvable formats that eliminate the chocking hazard some types of food pose to older adults with dysphagia. Along the same lines, Columbia University’s Creative Machines Lab is working to harness the precision 3D printing technology affords to create specifically formulated food items and vitamins that can be tailor-made to suit an exact individual’s nutritional needs. If such a machine were to be widely available for at-home usage, it’s not a huge conceptual leap to envision a marketplace emerging for 3D printing recipes and potentially for 3D printing at home to usurp restaurants as the “hands off” dining method of choice. The prospect of printing your family’s dinner may seem like science fiction right now but within a few years that may be a very real possibility.
Textiles
In 2016, Danit Peleg, a Tel Aviv-based designer, used 3D printing to create the dress that American snowboarder Amy Purdy wore at the opening ceremony of the 2016 Paralympic Games in Rio de Janeiro. A champion 3D printing in fashion, Peleg likens the textile industry to the music industry in terms of the potential for a digital revolution: “We used to buy CDs, and we had to go to the physical stores to get music and now we can just download it everywhere,” she says. “I believe that the same thing will happen with fashion eventually — clothes will become more and more digital.” Peleg hopes that one day, people will be able to download and print her garments at home. As it stands now however, the feel of 3D printed clothing presents a significant obstacle. Unlike traditional clothing manufacturing, 3D printing is limited in terms of the materials with which it can construct textiles. Many traditional 3D printing materials are scratchy and uncomfortable feeling to those wearing them. Peleg endeavors to resolve that issue by using FilaFlex, a flexible rubbery material that is more forgiving and comfortable to wear. In addition, the FilaFlex material allows her to print more than just the dress, she is also able to print accessories like shoes and sunglasses. 3D printing in the fashion industry has even begun to take hold in the product lines of mainstream brands, like Adidas. In January of 2018, Adidas jumped on the 3D printing trend with their Futurecraft 4D shoe that is created with 3D printed soles, featured in the video below.
The Dark Side of 3D Printing
“With great power comes great responsibility” – originally uttered as part of a Spider-man comic, this quote holds true for 3D printing as well. With the near endless possibilities that this technology affords, there are inevitably some areas and applications that, while technically feasible, have generated contentious discussion on the grounds of morality, ethics, and law. One such topic is 3D printed guns.
3D x Guns: In 2013, Cody Wilson, a 25-year-old student at the University of Texas Law School, finished the “Liberator,”
his first fully printed pistol and published the 3D designs online. Just a few days (and over 100,000 downloads) later, the State Department demanded the files be taken down and ignited a legal battle that has raged for 5 years. Finally, on June 22nd of this year, the federal government settled with Wilson and set a course for 3D gun blueprints to be readily available online, but the debate in the public forum rages on. Should blueprints for 3D guns be available to the public? Should 3D printed guns be declared universally illegal? How do the 1st and 2nd Amendments play into these discussions? The topic continually provides fodder for spirited discussion and it’s easy to see why; 3D printed guns exist in a murky and notoriously contentious area of the law that has sparked debates for decades.
For 30 years, the Undetectable Firearms Act (UFA) has set boundaries for firearm production, mandating that all firearms must be detectable by machinery calibrated to detect at least 3.7 ounces of steel. This mandate is problematic for most 3D printing producers because unless you want to spend upwards of $100,000 for a 3D printer that can print metal, plastic or other undetectable materials will generally be the mediums in your toolkit. Rather than make the substantial investment in hardware, many at-home producers opt to print the vast majority of the functional elements of the gun with cheaper plastic and then simply add a 3.7 ounce non-functional piece of steel to the finished product making it technically not illegal. While this does conform to the letter of the law, the degree to which it conforms to the spirit is largely left in the hands of the at-home manufacturer and user of the print.
Unlike with traditionally manufactured guns, the metal portion of a 3D print can be removed without removing any functionality from the gun. Ultimately, this leaves the decision of whether or not to conform to the law largely up to each individual user. That coupled with the fact that DIY 3D printing removes serial numbers and other identifying or tracking mechanisms from the equation, leaves us with a tool that has a large potential for abuse. Unfortunately, even assuming the vast majority of the members of our society are benevolent law-abiding citizens, when you take into account the destructive potential of a gun, it’s clear that even a tiny percentage of individuals with malicious intent can have a dramatic effect on the rest of the society.
3D x Drugs: Another divisive subject in the 3D printing world is 3D “Chemputers” and their ability to print drugs, both legal and illegal, from home. Chemputer, an amalgamation of the words chemistry and computer, is a term used by Glasgow University chemistry professor Lee Cronin to refer to his work developing a 3D printer that can use a combination of chemical compounds as “ink” to create individually tailored drugs.
While the ability to be able to create bespoke pharmaceuticals from the comfort of your own home would be revolutionary, that technology would also carry an inherent potential for abuse - what would prevent someone from using the printer to create illicit drugs or highly potent pharmaceuticals without a prescription? When posed that question, Cronin (seen above giving a TED talk on the subject) suggests that the future for obtaining digital drug “blueprints” could be regulated in the same way that Apple regulates which apps are allowed into its App Store. There could be some regulatory body that reviews all submissions and has checks in place to make sure that certain drugs are not allowed into the market and that drugs that require a prescription are not released to the user unless the prescribing doctor authorizes it. Even then, much like is the case with jailbroken Apple devices, there would likely be ways around the regulations. The extent to which those future devices can be exploited will likely have a significant impact on the overall feasibility of the technology.
3D x Counterfeiting: The ability to take a digital document and transform it into a physical, 3-dimensional one opens up a whole new avenue for black market trade and may begin to affect designer brands much in the same way that illegal downloading has affected the music industry. The Pirate Bay, one of the most notorious file-sharing sites, has already begun to cater to the 3D printing community with a category called “Physibles” through which its users can download 3D printable documents for a variety of different applications.
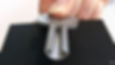
3D printers also have the potential to counterfeit other uniquely functional items like keys for houses, cars, and lockboxes. For most keys, the only thing a hacker needs to create a 3D printed replica is a simple image of the key like a picture captured on a smartphone. From that image, it is possible to construct a digital copy of the key that can be printed on even the cheapest of 3D printers. Luckily, there is already work being done to counteract this threat and, ironically, it is being accomplished using the very tool that created the threat in the first place: a 3D printer. Alejandro Ojeda, a mechanical engineer and founder of the company UrbanAlps, devised the “Stealth Key” (pictured above) - a 3D printed titanium key that hides its unique combination of bumps and ridges beneath pair of narrow ledges, making it impossible to replicate by simply using an image. It is currently made using a 3D printing process known as selective laser melting (SLM), typically used to create high-strength components for jet engines and gas turbines. While effective, this process does take much longer than conventional key-cutting with the printing time totaling about a day. Peace of mind with this technology doesn’t come cheap – the key and lock together cost about $200.
3D x Hacking: 3D printing’s reliance on computers piqued the interest of five researchers across four universities and provided the impetus for “dr0wned,” a project that aimed to demonstrate security threats born of an over-reliance on computers. The goal of the project was to hack into 3D design files and maliciously alter them in such a way that would go undetected through production but would compromise the final product during use.
During the experiment, they targeted a propeller that was set to be 3D printed and used as a component in a drone. The project was ultimately a success, causing the drone to literally fall from the sky when the altered propeller broke apart in the air. This study raises some legitimate concerns about the security of 3D print manufacturing and the need to be conscious of the technology’s reliance on computers and to safeguard against malicious attacks. With new technology, comes new possibilities, and with new possibilities, come new exploits. This project accomplished the goal of bringing a consciousness of the technological vulnerability that is often present in 3D manufacturing to the forefront of the mindshare in the community which, as 3D printing takes more and more of a role in the manufacturing of everything from airplanes to skyscrapers, is of paramount importance to ensure safety for all.
Where is 3D Headed?
Driven by widespread research and development in a vast array of fields, the possibilities for 3D printing are near endless. World-renowned 3D printing experts Wohlers Associates revealed some impressive growth figures in the 2018 edition of their annual report on the 3D printing. Using the term “AM” to refer to additive manufacturing (a term synonymous with 3D printing) the Wohlers Report 2018 states:
“In 2017, the AM industry, consisting of all AM products and services worldwide, grew 21% to $7.336 billion. The growth in 2017 compares to 17.4% growth in 2016 when the industry reached $6.063 billion and 25.9% growth in 2015… The total industry estimate of $7.336 billion excludes internal investments from the likes of Airbus, Adidas, Ford, Toyota, Stryker, and hundreds of other companies, both large and small. A surprising number of the $1-5 billion companies – many of which are unfamiliar to most of us – are investing in AM R&D (research and development).” (Forbes’ coverage of the report, to purchase the report itself)
This rate of growth is expected to continue into the coming years; according to the International Data Corporation (IDC), a global provider of market intelligence, advisory services, and events for the information technology, telecommunications, and consumer technology markets, global spending for 3D printing is projected to reach $23 billion USD by the end of 2022.
Investments
It’s easy to see why the growth rate in the industry is what it is; countries and companies worldwide are recognizing the potential of 3D printing and are investing heavily. Legendary investor Warren Buffet and his company Berkshire Hathaway acquired aerospace parts manufacturer Precision Castparts for the gargantuan sum of $37.2 billion in 2016. This acquisition, to date, remains the largest in Buffet’s career. Swedish company Siemens is set to make a 30 million euro (US $34.2 million) investment in a new state-of-the-art 3D-printing factory. In 2016, General Electric revealed plans to invest $3.5 billion in additive manufacturing over the subsequent 5 years. GE has even created a special division for its work in 3D printing called GE Additive that is developing the world’s largest laser-powered 3D printer that prints parts from metal powder. And the list goes on from there.
National governments are also getting in on the action: The US is estimated to lead global spending in the industry in 2019 with an IDC-projected $5.4 billion in spending. Western Europe follows with a projected $4.0 billion and China comes in third with a projected spending total of $1.9 billion. Over the last 5 years, the UK has invested over 200 million pounds (US $255 million) into additive manufacturing and holds a 5 percent stake in the worldwide 3D printing market. The government of Holland in association with industry partners is slated to make a 134 million euro (US $150) investment in research projects focusing on 3D printing. China is investing in future generations by installing 3D printers in all of its 400,000 elementary schools within the next two years. In 2017, the Republic of Korea invested $37 million towards the development of 3D printing and established a framework for national research and development to keep up with the worldwide trend towards the technology. Saudi Arabia recently entered into a joint venture with Chinese 3D printing company WinSun to address a shortage of affordable housing. The project, valued at $1.5 billion, utilizes 100 3D printers that will be used to print up to 1.5 million homes using concrete printing technology.
3D printing is a fast-growing industry and it’s easy to see why; it is an incredibly versatile and increasingly cost-effective manufacturing method that is just starting to realize much of its potential on a worldwide stage. With global investment and an ever-increasing list of applications in a vast array of industries, the future is extremely bright for this revolutionary technology.